Mastering the Recruitment of Forklift Operators
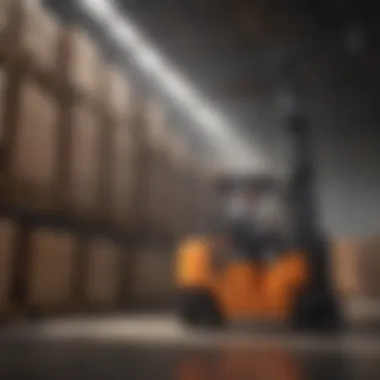
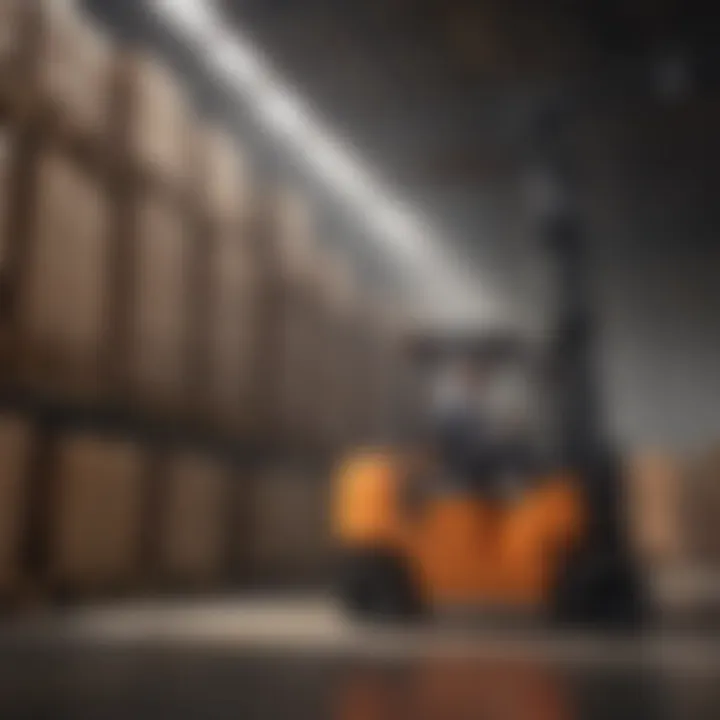
Intro
In todayโs warehousing and logistics sectors, hiring qualified forklift operators has become crucial for smooth operations. This process demands a comprehensive understanding of both the requirements and practices that dictate successful recruitment. As forklifts play an essential role in material handling, the competence of those operating them directly impacts efficiency and safety in the workplace.
It is vital to grasp the significance of employing proficient forklift operators who are equipped with necessary skills and knowledge to operate the equipment securely. Regulatory compliance, especially concerning OSHA regulations, cannot be overlooked. Moreover, advancements in technology, such as automation and improved training methods, are shaping the future of hiring in this field.
This article aims to consolidate insights and guidance to enhance the understanding of hiring processes for forklift operators. By diving into essential considerations, safety measures, technological impacts, and assessment methods, organizations can refine their recruitment strategies and ensure they select the best candidates.
Prolusion to Forklift Operations
Understanding forklift operations is essential for companies relying on effective material handling. Forklifts play a crucial role in various sectors, from warehouses to construction sites. They facilitate the movement of goods, making processes efficient and timely. As industries evolve, so does the need for skilled forklift operators. Therefore, hiring the right professionals is vital to operations.
Forklift operators are not just equipment handlers; they are pivotal to ensuring safety and productivity in workplaces. Their actions can significantly impact not only operational efficiency but also compliance with safety regulations. This section explores the foundational aspects of forklift operations, which forms the backbone for recruitment strategies.
Definition and Purpose of Forklifts
Forklifts are industrial vehicles designed to lift, move, and stack materials in various environments. Their main function is to handle heavy loads, which might be too cumbersome for manual labor. Forklifts increase efficiency in the movement of goods, minimizing physical strain on workers and reducing time spent on manual handling.
The purpose of forklifts goes beyond mere lifting. They are integral to warehouse management, construction, manufacturing, and many other fields. Their versatility allows for the handling of diverse materials, including pallets, crates, and large machinery parts. A well-operated forklift can enhance workflow and contribute to the bottom line of a business.
Roles of Forklift Operators in Various Industries
Forklift operators play distinct roles depending on the industry they serve. Each sector has its own specific requirements for the safe and effective use of forklifts. In warehouses, operators manage the storage and retrieval of goods, optimizing space efficiency. In construction, forklift operators might assist in moving building materials, ensuring that supply chains run smoothly.
The responsibilities of forklift operators include:
- Load Management: Ensuring that the loads are balanced and secure before lifting.
- Equipment Maintenance: Performing basic checks and upkeep on the forklifts to prevent malfunctions.
- Safety Protocols: Adhering to safety regulations and protocols during operations to minimize risks.
- Coordination: Collaborating with other personnel to avoid accidents and facilitate efficient workflows.
In summary, forklift operators are key players in maintaining operational effectiveness across various industries. They ensure the reliability of material handling processes and contribute significantly to overall workplace safety.
Skills and Qualifications Required
Hiring forklift operators requires a comprehensive understanding of the necessary skills and qualifications. Assessing these attributes is crucial for ensuring that operators can perform effectively and safely. The complex nature of forklift operation demands a blend of technical knowledge, practical skills, and compliance with safety regulations. This section emphasizes the essential competencies of forklift operators, focusing on their significance in the hiring process and long-term operational success.
Essential Skills for Forklift Operators
The role of a forklift operator involves much more than simply moving loads. Operators must exhibit both technical skills and cognitive abilities to navigate challenges on the job. Here are key skills necessary for effective forklift operation:
- Technical Proficiency: Operators must fully understand how to operate various types of forklifts, including counterbalance, reach, and rough terrain models.
- Spatial Awareness: A solid sense of space is vital to maneuvering effectively in congested areas, minimizing risks of accidents.
- Attention to Detail: Operators must conduct pre-operation inspections to ensure equipment is safe and ready for use. Missing a critical fault could result in accidents.
- Time Management: Operators often work under tight schedules. They should efficiently prioritize tasks while maintaining high safety standards.
Employing operators with these skills not only enhances productivity but also fosters a culture of safety and efficiency within the workplace.
Educational Background and Experience
While formal education may not be mandatory, relevant experience and knowledge play a significant role in hiring decisions. Candidates with experience in warehouse or industrial environments tend to better understand the workflow and associated challenges. Key points regarding educational background include:
- High School Diploma or Equivalent: Most employers prefer operators who have completed high school.
- Relevant Experience: Prior experience operating forklifts and familiarity with warehouse logistics can enhance a candidate's chances of being hired.
Employers should look favorably on candidates with hands-on training or apprenticeships, as these experiences provide practical insights into forklift operation and safety protocols.
Certifications and Licenses
Certifications are essential in validating an operator's capabilities and ensuring compliance with safety regulations. In the United States, the Occupational Safety and Health Administration (OSHA) mandates that forklift operators receive proper training and certification. Key certifications include:
- OSHA Forklift Operator Training: This certification confirms that operators have undergone necessary safety training and understand operational protocols.
- Additional Certifications: Depending on the industry, certifications specific to electric, propane, or specialized forklifts may also be beneficial.
Having certified operators leads to reduced liability for employers, improved safety records, and an overall more competent workforce.
"Employers must prioritize hiring certified forklift operators to ensure compliance with OSHA regulations and promote a safe working environment."
In summary, the combination of essential skills, appropriate educational background, and relevant certifications creates a strong foundation for successful forklift operation. Prioritizing these factors in the hiring process not only supports safety and efficiency but also contributes to organizational success.
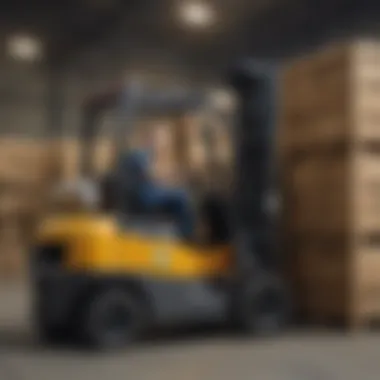
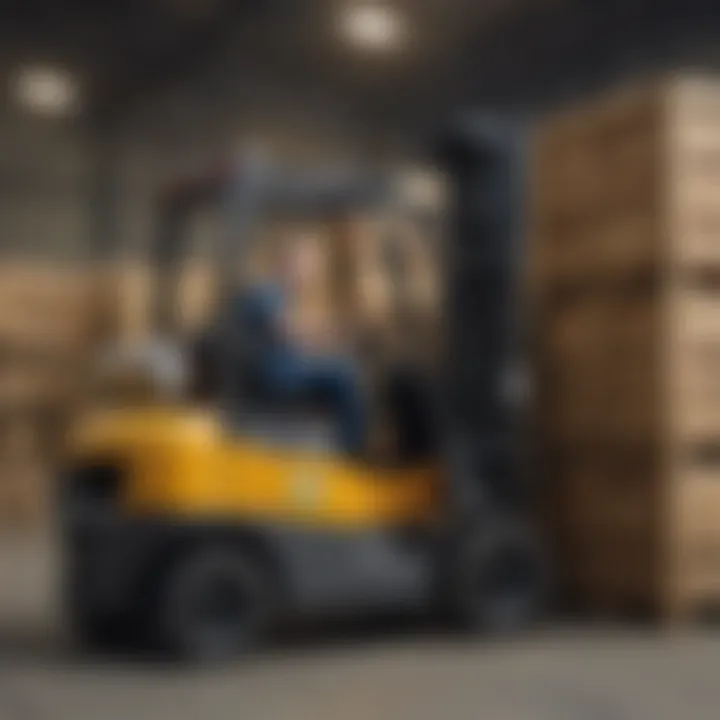
Regulatory Considerations
Understanding the regulatory considerations is essential for any organization seeking to hire forklift operators. These regulations not only dictate the framework within which operators must work but also help ensure safety and efficiency in the workplace. Moreover, compliance with these regulations is a legal requirement. Failing to adhere can lead to serious consequences, including fines, accidents, and even legal action. Therefore, being well-informed about these regulations is invaluable to both employers and employees in the forklift operation sector.
OSHA Regulations Affecting Forklift Operation
The Occupational Safety and Health Administration (OSHA) sets forth stringent regulations impacting forklift operations. Compliance with these regulations is not voluntary; it is mandatory. OSHA standards require employers to ensure that operators are properly trained and certified, safeguarding workplace safety.
Some critical OSHA regulations regarding forklift operation are:
- General requirements for powered industrial trucks, which include design and maintenance standards.
- Operator training and evaluation guidelines, which dictate that employers must ensure operators are competent in both knowledge and skills.
- Daily equipment safety checks that operators must perform to identify potential hazards before beginning work.
By adhering to OSHA regulations, companies can significantly reduce incidents of workplace accidents. As a result, they protect not only their workforce but also minimize potential financial liability.
Safety Training Requirements
Safety training is a cornerstone of the forklift operator hiring process. It is not enough to hire operators based solely on their experience; they require specific safety training tailored to the operational standards of the workplace.
Employers must ensure training includes:
- Comprehensive instruction on equipment handling and control functions.
- Hazard recognition training, which teaches operators how to identify and mitigate risks present in the work environment.
- Emergency procedures that outline how to safely react in case of an emergency situation while operating a forklift.
Regular refresher courses and up-to-date training are also recommended to keep the workforce informed about the latest regulations and technologies. Ongoing training reinforces safe operating techniques and encourages a culture of safety within the organization.
"Following OSHA regulations and maintaining rigorous safety training can lead to safer work practices and reduced injury rates in forklift operations."
By structuring the hiring processes around these regulatory considerations, organizations can both comply with the law and create a safer work environment for their employees.
Hiring Process Overview
In the competitive landscape of forklift operations, a well-defined hiring process is crucial. It ensures that organizations not only select skilled candidates, but also comply with industry regulations and meet workplace safety standards. This stage sets the framework for identifying and recruiting proficient forklift operators.
A structured hiring process helps in establishing clear expectations and roles. Each step outlined in this section plays a vital part in attracting capable candidates while minimizing the risk of hiring errors. This is particularly important considering how vital forklift operators are to operational efficiency and safety.
Developing a Job Description
Creating a detailed job description is the first step in the hiring process. It is more than just a list of responsibilities. The job description should communicate the specific duties associated with operating forklifts, along with the skills required. It is beneficial to outline the physical demands and work environment associated with the role.
Including key elements such as:
- Job Title: Clearly specify the position as "Forklift Operator".
- Responsibilities: Detail daily tasks, like operating forklifts, performing safety checks, and maintaining equipment.
- Skills: Mention essential skills such as attention to detail, safety awareness, and proficiency with forklift controls.
- Requirements: Include necessary certifications, such as OSHA Forklift Certification, and any prior experience if applicable.
This clarity not only attracts suitable candidates but also serves as a reference throughout the hiring process.
Sourcing Candidates
Finding the right candidates often requires a multifaceted approach. Various channels can be used to source applicants effectively. Popular methods include:
- Job Boards: Websites like Indeed and Glassdoor allow employers to post job advertisements widely.
- Local Vocational Schools: Many schools offer training programs for forklift operation. Collaborating with these institutions can yield candidates who are freshly trained.
- Social Media and Online Platforms: LinkedIn can be a valuable resource for connecting with potential candidates who possess the right qualifications.
Networking within industry-specific groups, both online and in person, can also help uncover talent. Building relationships with other professionals can lead to referrals, which often result in more reliable candidates.
Resume Screening Techniques
After gathering applications, efficient resume screening is key. A systematic approach is essential to manage the volume of resumes received. Start by filtering out candidates who do not meet the minimum requirements listed in the job description.
Consider the following techniques:
- Keyword Searches: Use specific terms related to forklift operation to identify resumes that match the qualifications.
- Experience Relevance: Focus on relevant work history, especially previous roles as forklift operators or in similar environments.
- Certifications: Verify the presence of necessary certifications early in the screening process.
This approach narrows down the candidate pool to those best fitting your needs, ensuring a more efficient selection process.
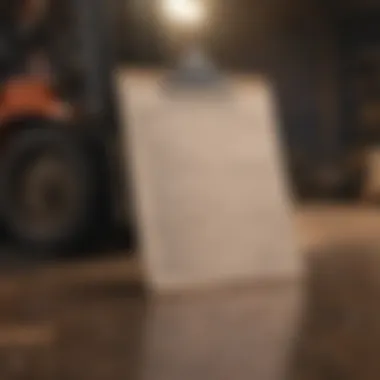
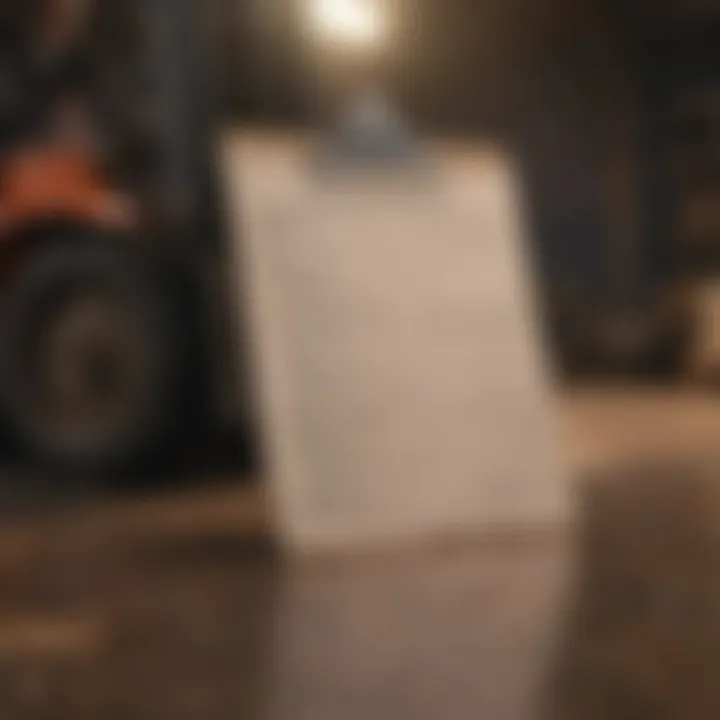
Interviewing Candidates
The interview stage is where insight into a candidate's suitability is further assessed. Prepare a set of structured questions that address both technical competence and behavioral traits. Key areas to explore during interviews include:
- Operational Knowledge: Ask about prior experiences with specific forklift models.
- Safety Awareness: Pose scenario-based questions to assess the candidate's awareness of safety protocols.
- Team Player Attitude: Understand how candidates work within a team and follow directions from supervisors.
Incorporating practical assessments during the interview can also be beneficial. For instance, evaluating a candidate's ability to conduct a pre-operation checklist can demonstrate their commitment to safety as well as their practical skills.
Effective hiring is not just about filling a position; it is about finding individuals who contribute to the organization's culture and operational success.
Assessment and Selection
Assessment and selection are critical components of the hiring process for forklift operators. These phases ensure that the candidates not only have the required skills but also fit the company's culture and operational needs. Conducting thorough assessments helps to avoid costly hiring mistakes, which can arise from selecting individuals who do not meet performance expectations.
One important benefit of effective assessment is that it identifies candidates who can operate forklifts safely and efficiently. Forklift operations can be hazardous; thus, ensuring operators have practical skills and a good understanding of safety measures is paramount for workplace safety. This selection process ultimately promotes a safer working environment and reduces the risk of accidents, which is vital within any industry that utilizes heavy machinery.
Additionally, assessment methods can also provide valuable insights into a candidateโs problem-solving abilities and their capacity to respond in high-pressure situations, which are commonplace in forklift operations. Selecting individuals who demonstrate strong situational awareness can lead to improved productivity and reduced liability for employers.
Practical Skills Testing
Practical skills testing is a hands-on approach to evaluate a candidate's capability to operate a forklift. This form of assessment is essential for validating that the candidate has the requisite motor skills and reflexes needed for operating forklifts under various conditions. Here are some important aspects of practical skills testing:
- Realistic Simulations: Candidates are often tested in controlled environments that simulate actual workplace conditions. This allows employers to assess their responses to common challenges encountered in their role.
- Observation by Experienced Personnel: It is beneficial to have experienced operators monitor and score candidates during tests. This layer of scrutiny helps ensure that evaluations are conducted fairly and accurately.
- Safety Compliance Checks: The testing must include assessing adherence to safety protocols. Proper use of PPE (Personal Protective Equipment), safety checklists, and emergency procedures should all be part of the testing framework.
Such comprehensive testing not only evaluates the technical skills of candidates but also reinforces the importance of safety culture in the workplace.
Behavioral Interviews
Behavioral interviews focus on understanding how candidates have responded to past experiences and challenges. This method aims to predict future behavior based on past actions. For forklift operations, this type of interview is highly relevant. Here are some key elements:
- STAR Method: Candidates can be asked to describe situations using the STAR (Situation, Task, Action, Result) method. This allows them to structure their responses clearly, showcasing their problem-solving skills and how they handle various scenarios.
- Scenario-Based Questions: Interviewers can present hypothetical situations related to forklift operations, asking candidates how they would react. This helps gauge their critical thinking, decision-making, and ability to handle stress.
- Team Interaction: Forklift operators often work as part of a team. Questions that explore how candidates have communicated or collaborated with others provide insights into their interpersonal skills.
By integrating behavioral interviews into the selection process, employers can better understand how candidates might perform in actual job situations, enhancing the overall quality of the hiring decision.
The Role of Technology in Hiring
In recent years, the adoption of technology has transformed the hiring landscape across many industries, including the domain of forklift operations. The integration of software and online platforms not only streamlines the recruitment process but also enhances the quality of hires. Companies now leverage various tech-driven solutions to improve efficiency, accuracy, and safety in their hiring practices, catering to an evolving market demands and regulatory pressures.
One significant aspect of this technological shift is its ability to manage candidate pools more effectively. By utilizing advanced data analytics and automated systems, hiring managers can access a broader range of applicants, facilitating a more thorough selection process. It also allows for faster communication, enabling employers to connect with suitable candidates without the delays often associated with traditional methods.
In this section, we will explore two key elements of how technology plays a role in hiring forklift operators: online training programs and applicant tracking systems.
Online Training Programs
Online training programs have emerged as a vital component in the onboarding process for forklift operators. These platforms facilitate convenient access to training materials, ensuring that candidates develop the essential skills required for safe operations. With remote learning possibilities, it allows prospective operators to complete their training at their own pace, which is particularly beneficial for individuals balancing other obligations.
The programs not only cover operational efficiency but also delve into safety protocols, regulatory compliance, and best practices. Key features of online training programs include:
- Flexibility: Candidates can engage with training modules at times that suit their schedules.
- Comprehensive Content: Encompassing various aspects of forklift operation and safety.
- Assessment Tools: Quizzes and exams to evaluate understanding of the subject matter.
- Certification: Upon completion, many programs provide digital certificates that can be shared with potential employers.
By prioritizing online training solutions, organizations can ensure a consistently high level of preparedness among their forklift operators. The result is not only a more competent workforce but also enhanced safety standards in the workplace.
Applicant Tracking Systems
Another crucial element in modernizing the hiring process is the implementation of applicant tracking systems (ATS). These systems are designed to streamline the resume screening and selection process, allowing employers to sort through applications efficiently. Utilizing an ATS can significantly alleviate the administrative burden of hiring teams, promoting a more systematic approach to recruitment.
Some noted advantages of utilizing ATS include:
- Automated Screening: The ATS can filter applications based on predetermined criteria, ensuring that only the most qualified candidates are advanced in the hiring process.
- Centralized Database: Maintaining a repository of candidate information simplifies retrieval and reduces the risk of losing valuable records.
- Collaboration Tools: Hiring teams can collaborate in real-time, sharing feedback on candidates and facilitating a more coherent decision-making process.
Investing in an effective ATS enhances the overall recruitment efficiency, allowing for better alignment of hires with organizational goals.
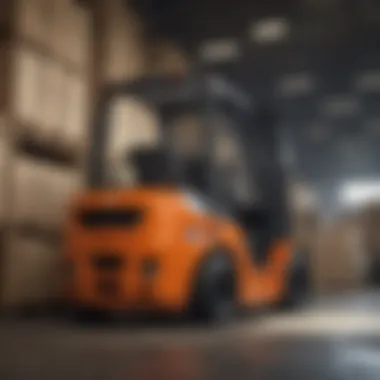
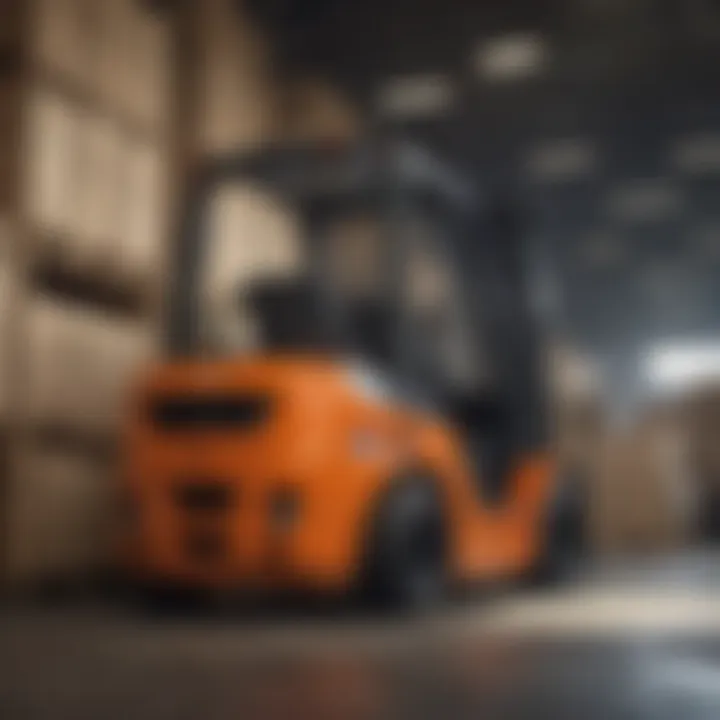
By embracing technology in the hiring of forklift operators, businesses are better suited to respond to the intricacies of the labor market. This shift not only addresses immediate needs but also sets the stage for ongoing efficiency in workforce management.
Safety Considerations Post-Hire
Safety considerations after hiring forklift operators are vital for maintaining a safe working environment. These elements ensure that operators are not only qualified but also consistently perform their duties in a safe manner. Proper focus on safety post-hire can significantly reduce workplace accidents, enhance productivity, and foster a culture of safety within the organization.
Ongoing Training and Compliance
Ongoing training is one of the key aspects of post-hire safety considerations. It is essential for operators to stay updated on safety protocols and equipment use. Regular training sessions should cover new safety regulations, operational best practices, and refresher courses on handling specific forklifts. This helps reinforce the importance of safety and ensures compliance with OSHA regulations.
Additionally, training should be tailored to the specific environments where forklifts are operated. For example, an operator working in a warehouse setting may face different challenges compared to one operating in an outdoor construction area. Continuous education mitigates risks associated with changes in equipment and workplace conditions.
Furthermore, compliance with safety standards cannot be overlooked. Businesses must ensure that operators understand their responsibilities regarding health and safety regulations. Compliance checks help to identify areas needing improvement and foster accountability among operators. Regular audits can provide insights into operator adherence to safety protocols, which can lead to a further reduction in incidents.
Evaluating Operator Performance
Evaluating operator performance is a critical part of ensuring ongoing safety in the workplace. Regular observations and assessments can help identify strengths as well as areas for improvement for each operator. Key performance indicators may include safe operation of equipment, adherence to safety protocols, and success in completing tasks without incidents.
Feedback mechanisms should be established to provide operators with constructive criticism. Consider using both informal discussions and formal evaluations to address performance issues. This creates an opportunity for operators to engage in discussions about their work environment, equipment challenges, and safety issues they might face.
Another important factor is to involve operators in the development of safety protocols. When operators contribute to safety discussions, it promotes a sense of ownership, leading to a more proactive approach to safety compliance. This collaborative environment encourages individuals to take accountability for their actions, thus enhancing overall workplace safety.
Continuous evaluation and training of forklift operators not only ensure compliance with safety regulations but also foster a culture of safety that benefits the whole organization.
In summary, post-hire safety considerations are essential for the ongoing success of any operation that utilizes forklifts. By prioritizing ongoing training, compliance, and performance evaluation, companies can create a safe work atmosphere that contributes positively to their operational efficiency.
Challenges in Hiring Forklift Operators
Hiring forklift operators is a complex task that comes with its own set of challenges. This is particularly true in industries that heavily rely on these operators for smooth operations. Understanding these challenges can enhance recruitment strategies and ensure that organizations make informed decisions.
High Turnover Rates
High turnover rates among forklift operators are a significant issue faced by many organizations. The nature of the job, which involves physical labor and long hours, often leads to employee dissatisfaction. Many operators may find the work monotonous or may seek better opportunities elsewhere. This challenge can be mitigated through several strategies:
- Competitive Compensation: Offering salaries that reflect the physical demands and skill level required can help attract and retain qualified operators.
- Career Development Opportunities: Providing pathways for advancement within the organization can encourage operators to stay longer.
- Positive Work Environment: Cultivating a supportive and respectful work culture decreases turnover by improving job satisfaction.
High turnover is costly, manifesting in frequent training costs and disruptions to operations. Therefore, strategies to maintain a stable workforce are essential.
Adapting to Technology Changes
Another challenge in hiring forklift operators is the rapid advancement of technology. Modern forklifts come equipped with various automated features and integrations that require operators to have specific skills. This necessitates continuous training and adaptability.
Hiring managers must consider the following:
- Training Programs: Implementing comprehensive training can help new hires adapt to new technologies efficiently.
- Skill Assessment: During the hiring process, assessing candidates' tech-savviness can ensure they are capable of managing sophisticated machines.
- Keeping Up with Trends: Regularly updating training material to reflect current technology ensures operators remain competent and confident.
"The pace of technological change is relentless; organizations must invest in their workforce continuously to keep up."
Understanding these challenges allows organizations to tailor their hiring processes, creating a more focused and strategic approach to recruit forklift operators. Knowing potential issues also guides the formation of policies that can enhance workforce stability and efficiency.
Finale
The conclusion serves as a crucial element in understanding the complex process of hiring forklift operators. It synthesizes the key insights and information presented throughout the article, reinforcing the importance of hiring practices in achieving operational efficiency and safety.
Summarizing Key Takeaways
In reviewing the hiring process for forklift operators, several key points arise:
- Regulatory Compliance: Understanding OSHA regulations is vital. These guidelines ensure all operators meet safety and operational standards, reducing workplace accidents.
- Skills Assessment: Identifying essential skills in candidates helps businesses select individuals who can perform effectively and safely in their roles.
- Technological Adaptation: Todayโs hiring processes often incorporate technology, enhancing efficiency in candidate tracking and assessment. Embracing this technology can streamline hiring workflows.
- Ongoing Training: Post-hire training is crucial for maintaining safety standards and adapting to changes in technology and regulations.
These takeaways align with the need for a thorough hiring strategy that encompasses regulatory knowledge, skill evaluation, and the strategic use of technology.
Future Trends in Forklift Operations
The landscape of forklift operations is evolving, influenced by several key trends:
- Increased Automation: Automation in warehouses is on the rise. Operators will increasingly need skills related to operating automated forklifts, pushing for retraining and adaptation.
- Data-Driven Decision Making: Hiring processes are leveraging data analytics. Tracking metrics related to hiring outcomes can refine recruitment strategies and improve employee retention.
- Sustainability Practices: As industries prioritize sustainability, the demand for electric and more eco-friendly forklifts is growing. Operators may require training specific to these technologies.
- Remote Work and Training: Remote training solutions are becoming more common, allowing for flexible training schedules and greater access to educational resources.
In summary, understanding the nuances of hiring forklift operators is essential for organizations aiming to maintain safety and efficiency in their operations. As trends evolve, adapting to these changes will be key in preparing operators for the future.