Essential Warehouse SOPs for Efficiency and Safety
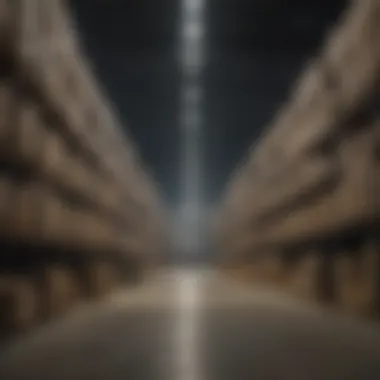
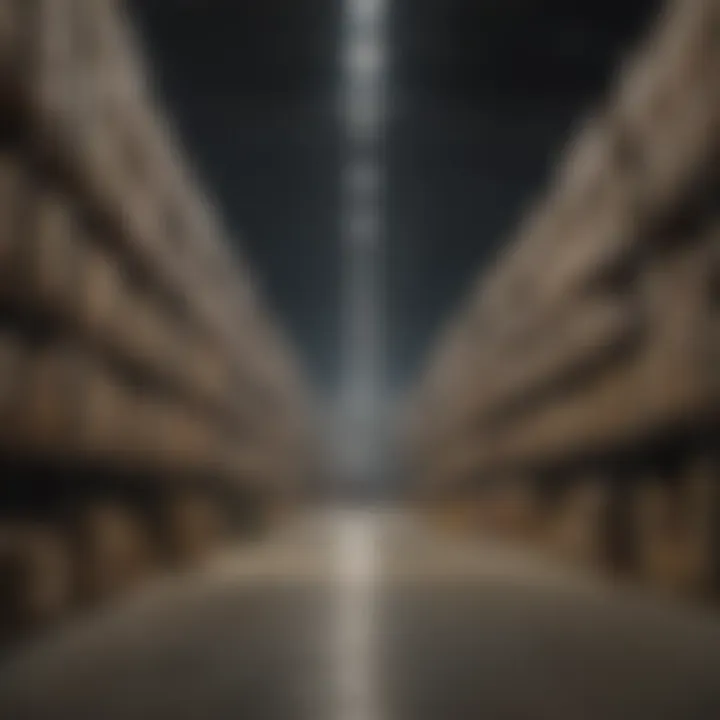
Intro
Warehouse Standard Operating Procedures (SOPs) play a crucial role in streamlining operations within warehousing environments. As businesses strive for operational efficiency and safety, understanding and implementing effective SOPs becomes paramount. This guide aims to explore the intricacies of SOPs, highlighting their significance, components, and best practices in the context of agriculture and horticulture. In addition, we will emphasize the importance of compliance and technology in developing robust procedures.
Topic Overview
Definition and Importance
Warehouse SOPs are documented processes that outline the steps necessary to perform specific tasks within a warehouse. These procedures establish consistency, reduce errors, and enhance worker safety. In the agricultural sector, where the storage and distribution of goods can be complex, SOPs facilitate efficient operations, ensuring that products are handled correctly from receipt to dispatch.
The importance of SOPs cannot be overstated. They serve as a framework for training new employees, standardizing processes, and maintaining compliance with industry regulations. Effective SOPs can lead to reduced operational costs and improved productivity, ultimately benefiting the bottom line.
Brief History and Evolution
The development of SOPs in warehousing has evolved significantly over the years. Initially, operations were based on informal practices, leading to inconsistencies and safety concerns. As the industrial revolution progressed, the need for formalized procedures became evident. With advancements in technology and management techniques, SOPs began to incorporate systematic approaches, emphasizing efficiency and safety.
In recent years, the introduction of digital tools and technologies has further transformed SOP development and implementation. Digital workflows allow for real-time updates, improving adaptability to changing conditions within the warehouse environment.
Key Techniques and Innovations
Sustainable Farming Practices
Incorporating sustainable practices into warehouse operations is becoming increasingly important. Utilizing eco-friendly materials and procedures not only reduces environmental impact but also aligns with the growing demand for responsible farming. SOPs can include guidelines for waste management, recycling, and energy-efficient practices, promoting a sustainable culture within the warehouse.
Advanced Agronomic Technologies
Modern technology has introduced innovative solutions for warehousing, such as automation and robotics. SOPs should encompass protocols for integrating these technologies into daily operations. This integration enhances productivity, reduces labor costs, and minimizes human errors, all while ensuring that safety remains a priority.
Practical Applications
Step-by-Step Guides
Implementing effective SOPs requires clear, actionable guidelines. Here is a simplified step-by-step approach:
- Identify Operations: Determine which processes require standardization.
- Gather Input: Consult with employees and stakeholders to gather insights.
- Draft SOPs: Create clear and concise documentation of procedures.
- Review and Revise: Allow for feedback and make necessary adjustments.
- Train Staff: Provide training sessions to ensure understanding and compliance.
- Monitor Compliance: Regularly review practices to ensure adherence to SOPs.
Case Studies or Real-World Examples
Real-world examples illustrate the tangible benefits of effective SOPs. For instance, a large agricultural warehouse implemented SOPs focusing on safe handling and storage of fertilizers. After training staff, the warehouse saw a significant reduction in accidents and improved inventory management. This case underscores the value of SOPs in enhancing both safety and operational efficiency.
"Warehouse SOPs not only protect your assets but also safeguard your employees, creating a healthier work environment."
Understanding Warehouse Standard Operating Procedures
Effective warehouse management relies heavily on the principles outlined in Standard Operating Procedures (SOPs). Understanding these SOPs is key for achieving operational efficiency and enhancing safety within the warehouse environment. These procedures serve as a formalized guide that outlines the best practices for various tasks, minimizing errors and ensuring consistency across operations.
When we define SOPs in the context of warehousing, we recognize them as essential components that help streamline processes. Thus, it is vital to develop a clear understanding of these documents to ensure smooth operations and compliance.
Definition of SOPs in Warehousing
Standard Operating Procedures in warehousing refer to documented processes outlining how specific operations should be performed. These include step-by-step instructions for tasks such as receiving inventory, storing goods, picking orders, and shipping products.
SOPs are crucial in establishing a standard approach, which reduces variability and fosters a uniform operational environment. They ensure that employees follow prescribed protocols consistently, thus promoting safety and efficiency. Moreover, by laying out these guidelines explicitly, organizations can better train staff and hold them accountable for their actions in the warehouse.
Importance of SOPs
The importance of SOPs in warehouse management cannot be overstated. They play a significant role in ensuring safety, improving productivity, and facilitating compliance with regulatory standards.
- Safety: Properly documented SOPs provide guidelines on how to perform tasks safely. They minimize risks related to workplace accidents, especially when operating heavy machinery and handling hazardous materials.
- Consistency: Having a standard approach improves consistency across the workforce. This reduces the chance of errors that may arise from varying methods employed by different staff members.
- Training: SOPs serve as training tools for new employees, guiding them through their responsibilities without the need for extensive supervision. This efficiency aids in faster onboarding and competency in tasks.
- Compliance: In many industries, adherence to regulations is crucial. SOPs help warehouses maintain compliance with industry standards and governmental regulations, which can vary by sector and region.
- Operational Efficiency: By clearly outlining the best practices for tasks, SOPs identify inefficiencies and facilitate continuous improvement, thus promoting overall operational excellence.

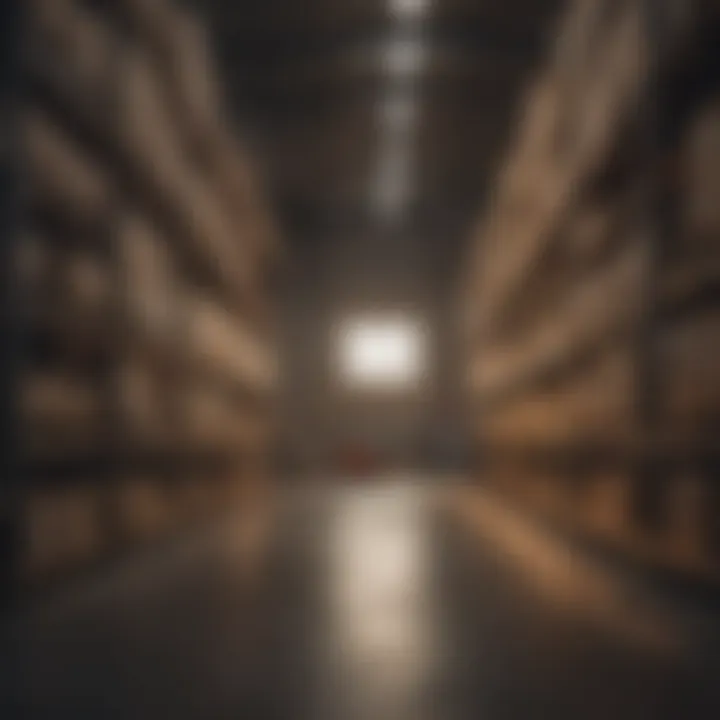
"Clear SOPs are an investment in time that pays dividends in efficiency and safety."
In summary, understanding warehouse SOPs is essential for ensuring all operations run smoothly. By defining and documenting procedures, organizations can promote safety, enhance productivity, and maintain regulatory compliance.
Key Components of Warehouse SOPs
The effective management of warehouse operations hinges on the clarity and precision of its Standard Operating Procedures (SOPs). These components serve as the backbone of daily activities, ensuring that all processes are executed correctly and consistently. Understanding these components is critical for maximizing operational efficiency, enhancing safety, and complying with industry regulations.
Safety Protocols
Safety protocols are essential in any warehouse environment. They establish guidelines for safe operations, minimizing risks that could lead to accidents or injuries. Proper safety protocols include the use of personal protective equipment (PPE), emergency response procedures, and regular safety drills. These measures not only protect workers but also contribute to a more productive atmosphere, as employees feel secure. In effect, implementing these protocols fosters a culture of safety that permeates all levels of an organization.
Inventory Management Procedures
Inventory management is a key area that dictates the flow of goods within a warehouse. Effective procedures help ensure that inventory levels are maintained, preventing shortages or overstock situations. Inventory management involves systematic tracking of stock levels, storage conditions, and stock rotation based on first-in-first-out (FIFO) principles. This approach reduces waste, especially in sectors dealing with perishable goods, such as agricultural products. Using automated inventory systems can enhance accuracy and efficiency, making them indispensable in contemporary warehousing.
Receiving Goods Process
The receiving process is the initial step in the supply chain that affects all subsequent operations. An effective receiving process includes verifying shipment contents against purchase orders, inspecting for damage, and properly documenting the receipt of goods. Accurate recording ensures that any discrepancies are addressed promptly, reducing potential errors in inventory. Proper procedures at this stage ensure that items are stored appropriately, facilitating smooth workflow in later stages such as order fulfillment.
Order Fulfillment Process
Order fulfillment is the process of picking, packing, and shipping orders to customers. A structured order fulfillment process is vital for maintaining customer satisfaction and operational efficiency. This process should clearly outline how orders are selected, packed, and readied for shipping. Integrating technology such as barcode scanning can streamline fulfillment and reduce human error. Clear guidelines in this section enhance speed and accuracy in delivering goods to customers.
Shipping Procedures
Shipping procedures provide guidelines for getting products to their final destinations. These procedures include preparing shipping documents, selecting carriers, and ensuring compliance with transportation regulations. Properly drafted shipping procedures can greatly optimize logistics by reducing shipping delays and costs. Additionally, keeping abreast of changes in shipping regulations is crucial for compliance and operational integrity. Ensuring that all shipping practices are transparent and efficient also helps build trust with business partners and customers.
"Warehouse SOPs are not just guidelines; they are essential processes that determine the efficiency and safety of operations."
In summary, the key components of warehouse SOPs form a comprehensive framework that governs various facets of warehousing. Each component plays a critical role in enhancing operational efficiency, protecting employees, and ensuring customer satisfaction. By establishing and adhering to these SOPs, warehouses can maintain a high standard of performance essential for success.
Steps to Develop Effective SOPs
Developing effective Standard Operating Procedures (SOPs) is a critical element in ensuring that warehouse operations run smoothly. A well-crafted SOP can unify processes, improve safety, and elevate operational efficiency. As such, implementing these steps will allow for a structured approach to SOP development, ultimately benefiting stakeholders involved within the agricultural and horticultural sectors. This section focuses on four main areas: conducting a needs assessment, involving stakeholders, drafting the SOP document, and the review and revision process.
Conducting a Needs Assessment
The first step in developing effective SOPs is conducting a needs assessment. Understanding the specific requirements of the warehouse environment is crucial. This involves evaluating current processes, identifying pain points, and determining performance gaps. A comprehensive assessment may entail gathering data through observations, interviews with staff, and reviewing existing documentation.
In some cases, specialized vendors might assist in this evaluation. The aim is to establish clarity on what needs to be addressed in the SOP. This could include aspects such as inventory discrepancies, safety incidents, or inefficiencies in order fulfillment. By pinpointing these areas, the SOPs become targeted, relevant, and actionable.
Involving Stakeholders
Involving stakeholders is a key factor in creating effective SOPs. These include warehouse staff, management, and other relevant personnel who can provide insights into daily operations. Engaging with them ensures that the SOPs are grounded in practical reality and not merely theoretical frameworks.
During this phase, it is beneficial to conduct workshops or focus groups where everyone can voice their opinions. This process can strengthen teamwork and create buy-in. When stakeholders are involved, they are more likely to follow the SOPs, knowing their input was valued. In addition, it fosters a sense of ownership over the processes outlined.
Drafting the SOP Document
After conducting a needs assessment and involving stakeholders, the next step is drafting the SOP document. This document should delineate clear, actionable steps for each procedure. Clarity and simplicity are vital; using straightforward language ensures that all staff can easily understand and implement the procedures.
Important aspects to consider when drafting include:
- Format: Use a consistent template to make the document easily navigable.
- Visuals: Incorporate flowcharts or diagrams to illustrate complex processes.
- Numbering: Number each step to avoid confusion.
Once drafted, the document serves as a foundation for training and operational execution.
Review and Revision Process
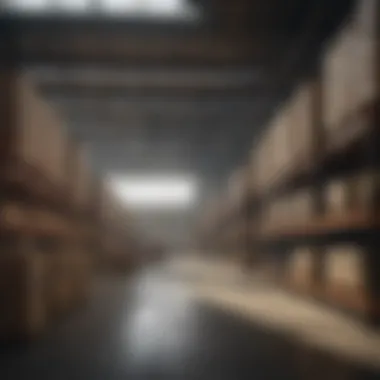
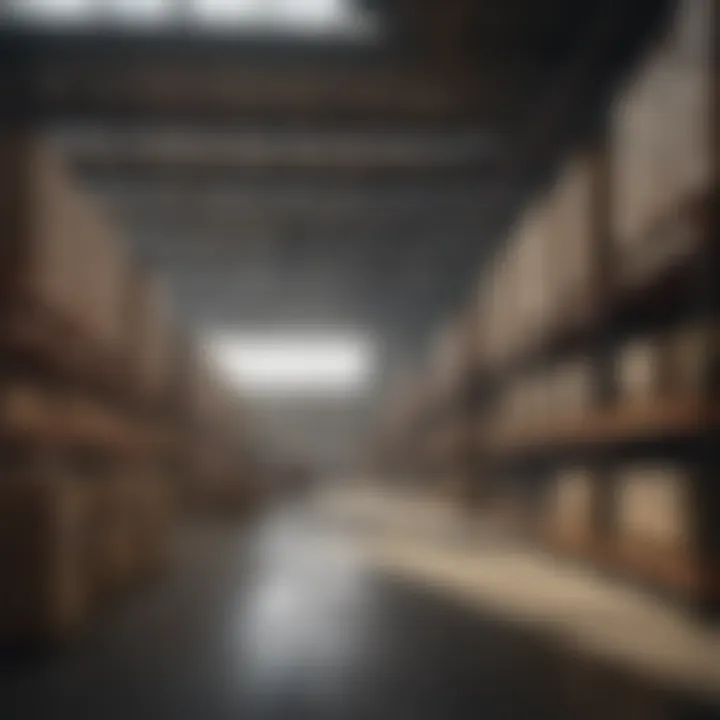
The last step in this process is the review and revision of the SOP document. This should happen periodically, or whenever significant changes occur in warehouse operations. Gathering feedback from users of the SOP is essential for ongoing improvement. Users can identify areas that might need updates based on their experiences.
It is worthwhile to implement a tracking system for changes and revisions. This documentation can help to maintain a historical record of how procedures have evolved, aiding future audits or assessments. Moreover, it allows continuous feedback for adaptation and improvement to stay aligned with industry best practices.
Training Staff on Warehouse SOPs
Training staff in warehouse standard operating procedures (SOPs) is essential for achieving operational efficiency and safety. Staff members are often the first line of defense against errors and risks. Proper training ensures they understand the protocols and the rationale behind them. This understanding leads to better adherence to procedures and reduces the likelihood of accidents.
Creating Training Materials
Effective training materials serve as the foundation for knowledge transfer. They should be clear, concise, and accessible. Key components of effective training materials include:
- Visual Aids: Diagrams and flowcharts can help illustrate complex processes.
- Written Guides: Detailed handbooks or manuals provide step-by-step procedures.
- Interactive Elements: Quizzes and checklists can engage learners and reinforce understanding.
When designing these materials, consider the diverse learning styles of staff. Some may prefer visual tools, while others benefit from hands-on practice. Additionally, keep language simple and avoid jargon to ensure clarity.
Conducting Training Sessions
The training session itself should be structured yet flexible. Start by outlining the goals and expected outcomes. This sets a clear agenda for participants. It is beneficial to incorporate the following elements in the training sessions:
- Demonstrations: Show staff how to perform specific tasks under real conditions.
- Group Discussions: Encourage questions and share experiences to enhance learning.
- Role-Playing: This technique can be useful for understanding procedures in a practical context.
Monitoring engagement during sessions is crucial. If staff seem disengaged or confused, it might be necessary to adapt the approach on the fly.
Evaluating Staff Understanding
Assessing staff comprehension after training is vital for ensuring that the objectives have been met. This evaluation can take various forms. Common methods include:
- Assessments: Short tests can gauge retention of material and highlight areas needing additional focus.
- Observation: Supervising staff as they execute tasks allows for immediate feedback and remediation.
- Feedback Forms: Collecting input on the training process helps identify strengths and weaknesses in the program.
Ongoing evaluation fosters a culture of continuous improvement. It also empowers staff by reinforcing their understanding of SOPs, which ultimately contributes to safety and efficiency in the warehouse environment.
Proper training transforms SOPs from mere documents into actionable practices vital for organizational success.
Ensuring Compliance with Regulatory Standards
Ensuring compliance with regulatory standards is a critical component of managing warehouse operations. This aspect fosters not only safety and efficiency but also enhances accountability and operational credibility. In a field where regulations can directly affect the human workforce and the integrity of goods, understanding these compliance requirements is paramount for any organization in the agricultural sector.
Understanding Relevant Regulations
Regulatory standards vary depending on geography, type of goods stored, and specific operational practices. For warehousing in agriculture, compliance often encompasses food safety laws, storage temperature regulations, and occupational health and safety standards.
For instance, in the United States, warehouses storing food products must adhere to the standards set by the Food and Drug Administration (FDA). The regulations involve proper tracking of inventory to ensure that all products are stored safely and within mandated environmental conditions. Understanding these regulations involves continuous monitoring of updates and changes in practices affecting the agricultural community.
- Maintaining awareness of changes in regulations helps prevent costly penalties and ensures ongoing operational viability.
Maintaining Documentation
To comply effectively with various regulations, maintaining thorough documentation is essential. This includes records of training sessions held for staff on safety practices, logs of equipment maintenance checks, and any incident reports that arise during operations. Proper documentation acts as both a shield and a guide for your organization, protecting against potential legal issues while offering insight into areas that may need improvement.
Here are some key points to consider about maintaining documentation:
- Standard Operating Procedures (SOPs): SOP documents must reflect current practices and be accessible to all staff members.
- Audit Trails: Keep comprehensive records of activities, which can be useful during regulatory inspections.
- Incident Reports: Document any accidents or near misses to identify patterns and prevent future occurrences.
Maintaining a structured approach to documentation helps streamline processes and supports better training for new employees, reinforcing a culture of accountability and compliance in your workforce.
The Role of Technology in Warehouse SOPs
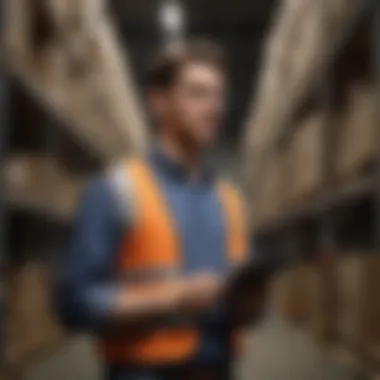
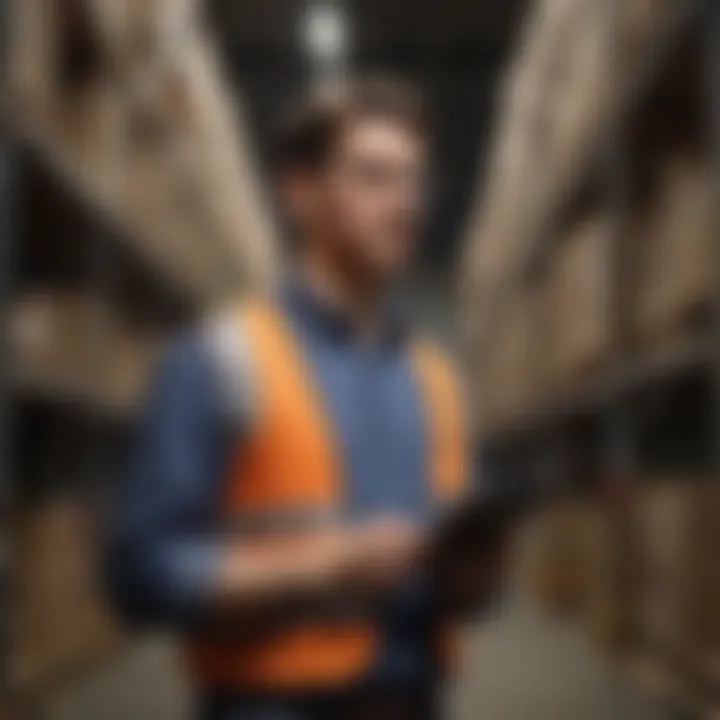
The incorporation of technology into Warehouse Standard Operating Procedures (SOPs) is crucial for enhancing operational efficiency and accuracy. Technology not only streamlines various processes but also ensures consistency in execution. In the highly competitive environment of warehousing, leveraging technology can lead to significant improvements in productivity and safety. Businesses that adopt advanced technological solutions tend to see better resource management, cost reductions, and an overall smoother workflow.
Automated Systems for Operational Efficiency
Automated systems play a pivotal role in optimizing warehouse operations. These systems include software solutions that facilitate inventory management, order processing, and shipment tracking. By deploying automation, companies can minimize human error while speeding up tasks that would typically require considerable manual labor. Automated guided vehicles (AGVs), barcode scanning technology, and advanced warehouse management systems (WMS) are examples of tools that enhance operational efficiency.
- Increased speed of order fulfillment.
- Reduction in labor costs and overtime pay.
- Enhanced accuracy in inventory counts and demand forecasting.
- Improved safety by minimizing manual handling of products.
"Automation is not just about replacing workers; it's about enabling them to focus on tasks that require human intellect."
These automated systems process large volumes of data instantaneously, allowing for real-time decision-making. For agricultural and horticultural warehousing, this means managing perishable items more effectively. Timely data and automation can prevent spoilage and ensure that products reach the market quickly.
Data Collection and Analysis
Data collection and analysis are fundamental to refining Warehouse SOPs. With modern warehousing increasingly relying on data analytics, businesses can obtain valuable insights that inform their strategies. Collecting data on inventory levels, order patterns, and shipment efficiency allows for a more informed approach in everyday operations.
Key benefits include:
- Predictive analysis: Understanding trends to forecast future demands, which is essential for effective inventory management.
- Performance metrics: Evaluating the efficiency of operations against predetermined standards, thus identifying areas for improvement.
- Cost analysis: Understanding where expenditures can be minimized without compromising quality or service.
Advanced data analysis tools utilize algorithms to help warehouse managers forecast demand, identify inefficiencies, and enhance customer satisfaction. By embedding data-driven decision-making into their SOPs, warehouses can adapt swiftly to changing market dynamics, preserving their competitive edge in the increasingly complex agricultural sector.
In summary, technology profoundly influences how warehouse operations are carried out. The integration of automated systems and robust data collection methods not only enhances operational efficiency but also positions organizations to thrive amidst challenges and opportunities.
Challenges in Implementing Warehouse SOPs
Implementing Standard Operating Procedures (SOPs) in warehousing is a crucial task that ensures operational harmony and compliance with safety standards. However, several challenges can impede this process. Understanding these obstacles is essential for agriculture farmers and enthusiasts seeking to optimize their warehousing operations.
Resistance to Change
One of the most significant hurdles in implementing SOPs is the resistance to change among staff. Humans naturally prefer established routines. When new procedures are introduced, there may be fears of increased workload or anxiety about adapting to unfamiliar tasks. This resistance can manifest in various forms, including passive non-compliance and active opposition to new processes.
To address this, involve employees early in the SOP development process. Gaining their input can create a sense of ownership and alleviate fears. Moreover, clearly communicating the benefits of the new procedures can encourage acceptance. Employees should understand how these changes will help streamline operations and enhance safety, ultimately leading to a more efficient workplace.
Strategies to Mitigate Resistance
- Engagement: Facilitate open discussions about the purpose of SOPs.
- Training: Provide thorough training to demonstrate new tasks.
- Support Systems: Establish mentorship programs where more experienced staff guide others in adapting.
Resource Constraints
Another prevalent issue is resource constraints. Implementing comprehensive SOPs requires time, money, and personnel that may not be readily available in some agricultural settings. Small-scale operations may struggle with the financial investment needed for development and training. Furthermore, staff shortages can limit the ability to create, implement, and review SOPs thoroughly.
To tackle these constraints, organizations can prioritize SOP implementation by focusing on critical areas first. Start with the most impactful procedures, such as safety protocols or inventory management. Finding cost-effective methods for training, like online resources and peer-led sessions, can also prove beneficial.
Tips for Overcoming Resource Constraints
- Phased Implementation: Introduce SOPs gradually rather than all at once.
- Leverage Technology: Use software tools for documentation and training to save time and resources.
- Collaboration: Work with local agricultural groups to share resources and knowledge.
Addressing these challenges head-on can significantly improve the chances of successful SOP implementation. By recognizing the factors affecting acceptance and resource availability, warehousing operations can be fine-tuned to better meet industry demands.
Continuous Improvement of SOPs
Continuous improvement of Standard Operating Procedures (SOPs) is essential for maintaining both productivity and safety in warehouse operations. As industries evolve, so do the practices and technologies that support them. Thus, updating and refining SOPs ensures they remain effective and relevant. This approach is not merely about reacting to change; it involves a proactive commitment to identify areas for enhancement. The aim is to facilitate a culture of ongoing refinement.
Collecting Feedback
Collecting feedback is a crucial element of continuous improvement in SOPs. Employees on the warehouse floor have firsthand experience with the procedures. Regularly seeking their input can reveal gaps, inefficiencies, or frustrations they encounter. This feedback can be collected through various methods, such as surveys, focus groups, or one-on-one discussions. Analyzing this information helps in pinpointing specific aspects of the SOPs that require attention.
Establishing a structured feedback mechanism fosters an environment where employees feel valued and heard. It reinforces the idea that their observations can drive procedural enhancements. Additionally, incorporating employee suggestions can result in better engagement and adherence to procedures, creating a more efficient workplace.
Adapting to Industry Changes
Industries do not remain static. Changes often arise due to technological advancements, shifts in consumer demand, or evolving regulatory frameworks. To maintain operational efficiency, warehouse SOPs must adapt to such changes. Evaluating industry trends and innovations is vital in making relevant updates to procedures.
Regular assessment of industry benchmarks helps to identify best practices. Aligning SOPs with these standards can improve productivity and compliance. Implementing changes based on industry insights signals to employees that the organization is committed to excellence.
In summary, continuous improvement in SOPs is a strategic necessity. Collecting feedback and adapting to industry changes are foundational elements of this process. They contribute not only to enhancing operational efficiency but also to fostering a positive organizational culture.