Essential Chicken Plucking Equipment Guide
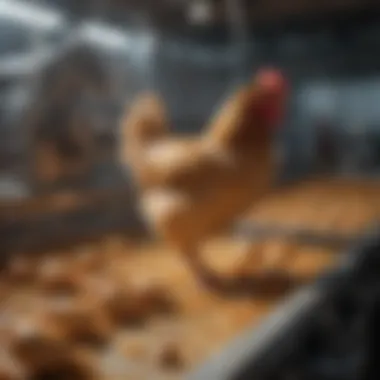
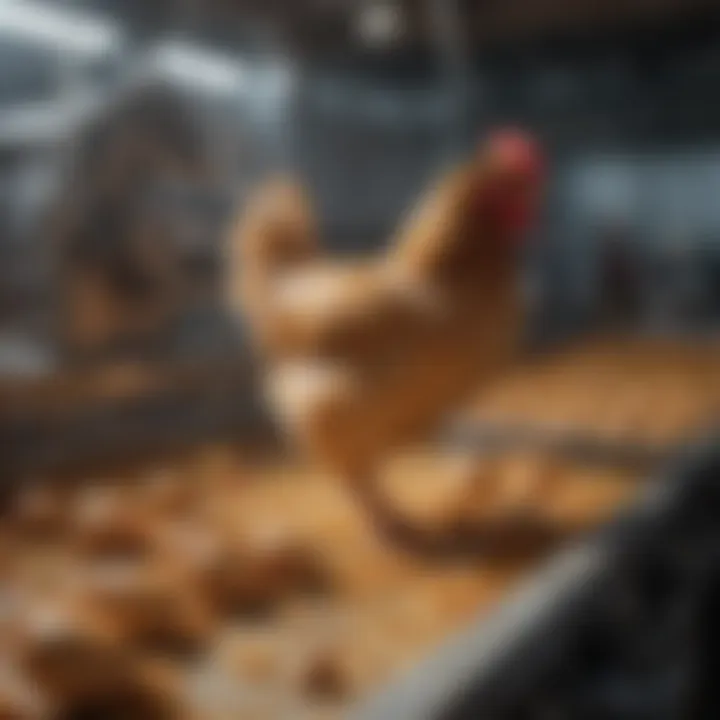
Topic Overview
Definition and Importance
Chicken plucking equipment plays a crucial role in poultry processing. At its core, this equipment streamlines the labor-intensive task of removing feathers from chickens, thereby enhancing the efficiency of meat production. As the demand for poultry rises globally, proper plucking machines are essential not just for speed but also for quality. Efficient plucking not only reduces the time it takes to process a bird but also helps maintain the integrity and presentation of the meat, which is a critical factor in marketing.
Brief History and Evolution
Historically, feather removal was a manual process, often done by hand, which proved to be laborious and inconsistent. Over the years, advancements in technology have transformed this sector. The introduction of the first mechanical pluckers in the early 20th century marked a significant shift in poultry processing methods. From simple drum-type machines to the automated systems we see today, the evolution of chicken plucking equipment mirrors broader technological advancements in agriculture. Modern machines are now designed with efficiency in mind, incorporating innovative features such as adjustable speed settings and automated feather removal processes, significantly improving productivity.
Key Techniques and Innovations
Sustainable Farming Practices
As consumers become increasingly aware of sustainability, chicken plucking equipment has also adapted to meet these demands. Modern machines can complement sustainable farming practices by reducing waste and energy consumption. Many machine manufacturers are exploring eco-friendly materials and energy-efficient technologies to enhance their products. Such advancements not only help in reducing the environmental impact but also appeal to a market that is increasingly prioritizing sustainability.
Advanced Agronomic Technologies
The rise of advanced agronomic technologies has shaped the design and functionality of chicken plucking machines. With features like smart sensors that monitor plucking efficiency and integrated software systems that track maintenance schedules, todayâs plucking equipment is more sophisticated than ever. This has allowed farmers and poultry processors to optimize their operations, ensuring that they are not only meeting the volume demands but also adhering to high standards of quality and safety.
Practical Applications
Step-by-Step Guides
To maximize the benefits of chicken plucking machines, operators should follow best practices when using and maintaining the equipment. Hereâs a simple guide:
- Choose the Right Machine: Assess the volume of poultry processing and select a machine that suits your needs. Consider aspects like capacity, designs, and technical specifications.
- Setup: Properly install the machine according to the manufacturer's instructions to ensure safe and effective operation.
- Operation: Load chickens into the machine without overcrowding. Monitor the plucking process to ensure even feather removal.
- Maintenance: Regularly check and clean the plucking components. Stay on top of routine maintenance to prevent downtime and issues.
Case Studies or Real-World Examples
Several poultry farms have successfully implemented modern chicken plucking machinery to enhance their operations. An example can be drawn from a Kentucky-based poultry processor that switched to a fully automated plucking system.
"The transition not only halved the plucking time, but it also improved the overall quality of our product. The machine adjusts to various breeds and sizes, making our process extremely versatile," shared the farm manager.
With advancements like this, many processors are reaping the benefits of integrating chicken plucking equipment that meets demands while ensuring a commitment to quality and sustainability.
Foreword to Chicken Plucking Equipment
The realm of poultry processing is one where efficiency, quality, and speed intertwine to create a successful farm operation. Within this landscape, chicken plucking equipment stands as a pivotal component. It's not just about removing feathers; it's about ensuring that the whole process flows seamlessly and effectively.
Overview of Poultry Processing
Poultry processing has evolved significantly over the years. Initially, it was a manual, labor-intensive task involving numerous steps from slaughter to packaging. However, modern methods have introduced specialized machinery designed to optimize each stage of production. The processing generally consists of several key stages: pre-slaughter handling, stunning, slaughtering, scalding, feather removal, evisceration, and packaging.
Each of these stages requires meticulous attention and appropriate equipment. Chicken plucking, specifically, has transformed from rudimentary tools to advanced mechanized processes. This evolution has not only reduced labor costs but has also heightened productivity, making it an essential focus for any poultry operation. The use of machines helps maintain consistent quality while minimizing the risk of injury to workers.
Importance of Efficient Plucking
Efficiency in plucking isn't just a matter of speed; it greatly influences overall production. A well-oiled plucking process can drastically reduce the time from farm to table. If feathers are removed swiftly and effectively, it allows for more birds to be processed within the same time frame, ensuring that the operation meets market demands.
Moreover, the quality of plucking directly affects the final product. Any remaining feathers post-processing can compromise the presentation of chicken, leading to customer dissatisfaction. An effective plucking system ensures that this issue is minimized.
Additionally, efficient plucking equipment can drastically cut down on labor costs, as fewer workers are required to achieve higher outputs. This becomes especially pertinent for those running larger-scale operations, where profit margins can hinge on operational efficiency.
"Investing in quality chicken plucking equipment not only enhances efficiency but also reflects a commitment to product quality."
The advances in technology have also played a role in improving the efficiency of plucking machines. Modern equipment comes equipped with features that allow for better control and adaptability, tailoring the plucking process to different bird sizes and types. In summary, understanding the importance of chicken plucking equipment is vital for anyone involved in poultry farming. This knowledge lays the groundwork for choosing the right machinery that aligns with operational goals and market expectations.
Types of Chicken Plucking Equipment
Understanding the various types of chicken plucking equipment plays a crucial role in optimizing the poultry processing workflow. As farmers or poultry processors, the choice between manual and mechanical methods can dramatically influence efficiency, labor costs, and ultimately, product quality. This section will explore those differences, discuss the distinct forms of mechanical pluckers, and provide insights into their unique attributes.
Manual vs. Mechanical Plucking
Manual plucking, while traditional, can be labor-intensive and time-consuming. Using hands or simple tools, workers pluck feathers one at a time, requiring significant human effort and often leading to fatigue. The appeal of this method lies in lower initial costs and no reliance on machinery. However, for larger operations, where efficiency is king, this method quickly becomes impractical.
In contrast, mechanical plucking utilizes machines engineered to automate feather removal. These machines not only save time but also improve consistency in plucking results. For poultry businesses aiming for scalability, mechanical plucking is an undeniable asset.
To sum it up:
- Manual Plucking:
- Mechanical Plucking:
- Higher labor costs over time.
- Lower initial investment.
- Suitable for small, niche farms.
- Reduced labor costs and fatigue.
- High initial investment but better returns in long run.
- Ideal for large-scale poultry operations.
Choosing between these methods depends largely on the size of the operation and specific goals in productivity and efficiency.
Types of Mechanical Pluckers
Mechanical pluckers come in various designs suited to particular needs. Here, we will look deeper into three predominant types: Drum Pluckers, Finger Pluckers, and Water Pluckers. Each type has its strengths and weaknesses, contributing differently to the overall plucking process and the quality of the final product.
Drum Pluckers
Drum pluckers are known for their efficiency and speed. These machines utilize a revolving drum covered with rubber fingers that glide over the chicken as it rotates, pulling feathers off in the process. The key characteristic of drum pluckers is their ability to handle multiple birds in a single batch, significantly speeding up the plucking process.
Their unique feature lies in the adjustable speeds at which the drum operatesâallowing users to optimize plucking based on the type of poultry being processed. However, a potential disadvantage is when not set correctly; drum pluckers might damage the skin or leftover pin feathers can become a hassle.
Finger Pluckers
Finger pluckers operate on a similar principle but use flexible fingers to pick feathers instead of a rotating drum. The key characteristic of finger pluckers is their gentleness during operation, making them suitable for delicate poultry processing. This type of plucker can adapt to various bird sizes and feather types, contributing greatly to flexibility in use.
A unique feature of finger pluckers is their ability to be manually adjusted for different feather densities. Yet, users should be aware that finger pluckers may be slower than drum models, requiring careful consideration of the processing volume.
Water Pluckers
Water pluckers take a different approach by incorporating heated water in the plucking process. After scalding, chickens are submerged in hot water, with specially designed nozzles that create a water stream that loosens and pulls feathers away. The key characteristic of water pluckers is this scalding process that not only aids in feather removal but leaves the skin undamaged and cleaner as well.
A unique feature of these machines is the potential for a more sterile processing environment, thanks to the heating elements. However, initial setup and maintenance of heating systems can be more complex and costly, which might not suit all operations.
In summary, understanding the differences among drum, finger, and water pluckers enables poultry farmers to make informed decisions that align with their operational needs and production goals. Typically, one size doesn't fit all, so itâs essential to evaluate the specific circumstances of each farm.
Mechanics of Plucking Machines
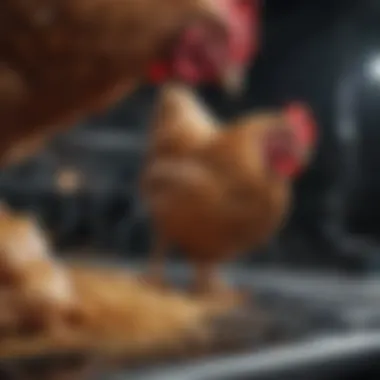
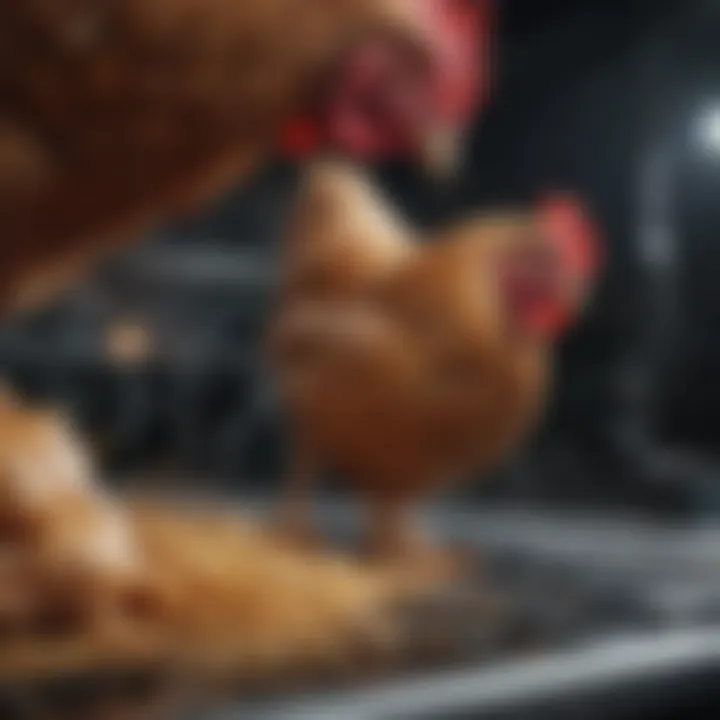
The mechanics behind plucking machines is crucial in understanding how these machines effectively remove feathers from poultry. Itâs a blend of intricate design and powerful engineering that allows farmers to achieve both efficiency and quality in their processing. This section delves into how the plucking mechanism fundamentally operates, alongside the key components that support its functionality. By examining these elements, one can appreciate the role they play in improving the overall plucking process.
Plucking Mechanism Explained
At the heart of any plucking machine is its plucking mechanism. This is essentially how the machine actually does its jobâremoving feathers quickly and effectively. Most machines utilize a combination of mechanical movement and friction to achieve the desired result. The feathers are dislodged when the chickens are gently tossed within the machine, while the plucking fingers or drum rotate at an optimal speed to make contact without damaging the skin.
The design puts a high premium on efficiency by minimizing the time required for plucking and maximizing output. A well-designed mechanism is essential. Not only does it affect the plucking speed, but it also determines the quality of the final product. An efficient mechanism ensures minimal feather residues are left behind, which can save on labor costs during inspection and cleaning stages.
Key Components of Plucking Equipment
The effectiveness of a plucking machine hinges on several key components, each contributing significantly to the machine's performance. Let's break these down further:
Motor Systems
The motor system is often regarded as the backbone of a plucking machine. This is the part that powers the entire unit, typically designed for durability and high torque, allowing it to handle vigorous operations. A key characteristic of motor systems in these machines is their ability to maintain a consistent speed under load, so plucking can be both rapid and efficient.
A notable feature of modern motor systems is their energy efficiency. Many machines are equipped with systems designed to reduce power consumption while maintaining output. The choice of motor can also influence the overall noise levels of the machine, which is an important concern for many operations. However, cheaper motors may lack longevity and could lead to higher repair costs in the long run, affecting its overall value.
Drum and Finger Configurations
Drum and finger configurations are essential for the actual plucking action. This design typically incorporates rubber fingers mounted on a rotating drum, which provide the necessary contact with the feathers. One key characteristic is the flexibility of these fingers; they can adjust slightly to conform to the contours of the bird when they are plucked. This is beneficial as it helps in removing feathers without damaging the skin beneath.
Moreover, some machines allow for interchangeable drums and fingers, giving operators the ability to tailor the setup according to the specific needs of their flockâlarger birds may require a different setup compared to smaller ones. However, it's worth noting that while finger configurations improve efficiency, if not replaced regularly, they can wear out, which may lead to poorer performance and higher maintenance issues.
Water Heating Elements
Water heating elements are present in certain types of plucking machines, particularly in water-based pluckers. The primary function of these elements is to heat water that is used in the plucking process. Heated water can loosen feathers more readily, enabling a cleaner plucking process and reducing damage to the poultry skin.
A key characteristic of water heating elements is their ability to quickly reach and maintain the required temperature for the best plucking efficiency. This is crucial as improper temperature settings can lead to feathering problems. A unique feature is the thermostatic control, which allows for precise management of heating levels. However, systems relying too much on water can risk water contamination; thus, proper filtration and regular maintenance are necessary to ensure machine longevity and hygiene.
In summary, understanding these mechanics and components of plucking machines not only enhances clarity on how they function but also aids poultry farmers in making informed choices. Choosing the right combination of design, motor systems, and configuration will ultimately affect productivity and the quality of the processed birds.
Selecting the Right Equipment
Selecting the right equipment for chicken plucking is crucial for any poultry operation. It can greatly influence the efficiency of the processing, the quality of the final product, and overall labor costs. Making informed choices not only optimizes workflow but also mitigates long-term expenses associated with maintenance and replacement. The type of equipment suited for a particular operation hinges on several critical factors that must be assessed before making a purchase.
Factors to Consider
When considering equipment for plucking, several elements come into play, each playing its own role in the effectiveness of the operation. Three key factors often highlighted are the scale of operation, budget constraints, and ease of use.
Scale of Operation
The scale of operation refers to how many chickens are being processed at a time. For smaller farms, a manual plucking setup may suffice, as it allows for flexibility without the high costs associated with larger machines. The benefit here is simplicity; manual plucking takes up less space and can be perfect for hobbyists or small-scale farmers.
However, larger operations will likely require more robust machinery. Here, a mechanical plucker could save both time and labor. The unique feature of a mechanical system is its capacity to handle larger volumes, enhancing throughput significantly. While the investment may be steep, it becomes a more beneficial option as production scales up. A small farm might find mechanical pluckers to be overkill, thus understanding the scale of operation is pivotal in choosing the right plucking equipment.
Budget Constraints
Budget constraints are a universal challenge for all farmers. It directly affects the choice of equipment available. The initial costs of mechanical pluckers can be daunting but, when viewed through the long-term lens of efficiency and reduced labor, they often prove themselves to be a sound investment.
A benefit of this consideration is that budget does not just cover the purchase price; ongoing expenses also come into play. Lower-priced equipment might save money upfront but could lead to increased maintenance costs and downtime. In contrast, higher-end machines may be more durable and efficient, translating to lower overall operation costs over time. Thus, being cognizant of the budget and its limitations remains a vital aspect of selecting plucking equipment.
Ease of Use
Ease of use relates closely to how intuitive the equipment is for the workers. Equipment that is easy to assemble, operate, and clean integrates better into daily routines. Simplicity often increases productivity, reducing the time spent on training and minimizing the chances of equipment malfunction due to improper handling.
Another characteristic tied closely to ease of use is the availability of support or resources for operators. For instance, robust user manuals, customer support, and online resources can make a considerable difference. The trade-off may be that less user-friendly machines often come with advanced features, but for many, the continuation of smooth operation is paramount.
Choosing the right equipment based on these factors can make the difference between a smooth operation and a constant uphill struggle.
Evaluating Brand Reputation
Brand reputation cannot be overstated when it comes to purchasing poultry equipment. Established brands tend to have a proven track record of reliability and customer satisfaction. Researching user feedback helps in understanding which brands offer premium service and support post-purchase.
Evaluating reviews on platforms, including Reddit, or consulting community discussions can also provide insight into how equipment holds up under real-world conditions. The reputation of a brand often correlates to the longevity of its products in a demanding environment. A reputation for quality can save a farmer from unexpected breakdowns and costly repairs in the future.
In summary, selecting the right equipment is a multifaceted process that demands careful consideration of scale, budget, ease of use, and brand reputation. By weighing these factors, farmers can equip their operations with machinery that suits both their needs and expectations.
Cost Considerations
Understanding the cost implications of chicken plucking equipment is paramount for anyone involved in poultry processing. From initial acquisition to ongoing maintenance, calculating costs accurately can mean the difference between a thriving operation and a struggling one. Moreover, with market fluctuations and technological innovations, itâs crucial to stay informed to make solid financial decisions that affect your livelihood.
Initial Investment
Every journey begins somewhere, and for many poultry farmers, the initial investment in equipment can feel like climbing a steep hill. Purchasing plucking machines, whether manual or mechanical, involves considerable capital. Prices can vary widelyâmanual pluckers might cost a few hundred dollars, while high-end mechanical versions can run into the thousands.
When weighing various equipment options, it's wise to consider the following:
- Operational Scale: For smaller operations, a manual plucker might suffice, cutting down on the initial cost. Those with larger volumes may need to invest in more sophisticated mechanical models.
- Quality vs Price: It can be tempting to go for the cheapest option, but low-quality machines can lead to higher costs down the line due to inefficiency or frequent breakdowns.
- Return on Investment: A good way to justify an expenditure is to estimate how quickly it will pay for itself in terms of saved labor and time.
In summary, the initial investment should be thought through with future growth and needs in mind. A penny saved now might cost you a dollar later if you choose poorly.
Long Term Maintenance Costs
The journey doesnât end with the purchase. Long-term maintenance costs can often be overlooked but are just as crucial. The bottom line is that keeping your equipment in working order is not just about fixing breakdowns. Itâs about regular upkeep and planning for eventual replacements or enhancements.
Several factors come into play when considering these costs:
- Routine Maintenance: Regular checks and tune-ups can prevent more significant issues later. This includes inspecting motors, cleaning out components, and checking for wear and tear.
- Parts Replacement: Even the best equipment will need parts replaced occasionally. Knowing which parts are susceptible to wear and how much they cost can help you budget adequately.
- Downtime Costs: When machines break down, youâre not just losing production time. This downtime translates to lost revenue, making it imperative to maintain equipment properly.
In the end, understanding both the initial costs and ongoing maintenance expenditures can provide a clearer picture of the total investment needed. As the saying goes, "A stitch in time saves nine." Investing in proper care now might spare you from larger headaches down the road.
"Calculating both the initial and long-term costs can provide the foundation for making informed decisions in purchasing plucking equipment."
Additionally, those involved in agriculture may find themselves reviewing resources or communities for insights, such as Wikipedia or Reddit, where industry discussions often surface valuable tips!
By taking these financial aspects into account, poultry farmers can not only equip themselves with the right machines but also ensure they sustain profitability well into the future.
Operational Guidelines
Operational guidelines serve as the backbone for any effective poultry processing facility. They're more than just a set of instructions; they are critical for ensuring the safety, efficiency, and overall effectiveness of chicken plucking operations. Ignoring these guidelines can lead not only to inefficiencies but also to safety hazards that could jeopardize the workers and the quality of the final product. Understanding operational protocols is paramount for any farmer or enthusiast who wants to stay ahead in the poultry business.
Preparing the Equipment for Use
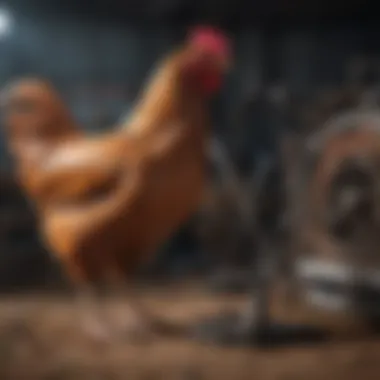
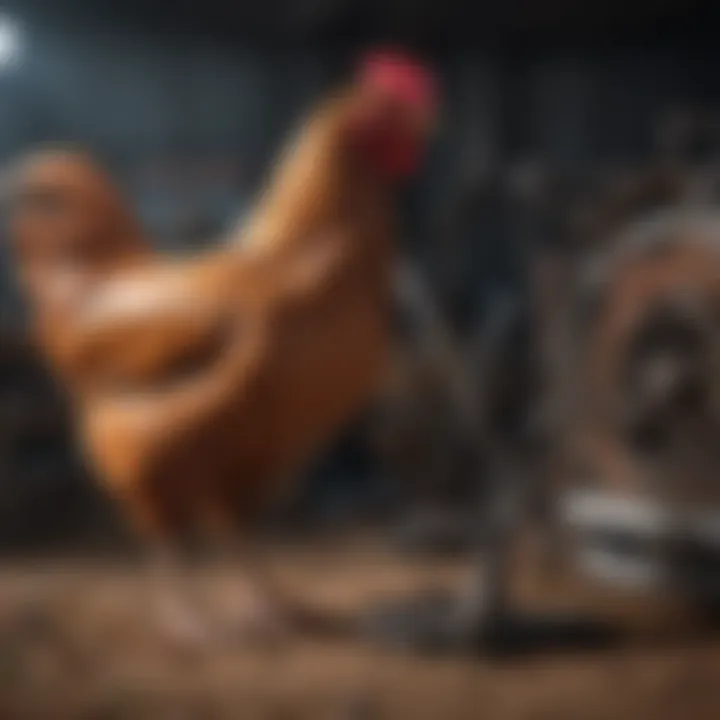
Before the first feather flies, one must prepare the equipment adequately. This step is crucial, as proper preparation minimizes potential downtime and maximizes productivity. Here are some points to consider:
- Inspection: Always check the machine for any wear or damage. Look for loose screws, frayed wires, or any visible wear that could lead to bigger issues down the line.
- Cleaning: Ensure that the plucker is thoroughly cleaned. Scraps from previous operations can accumulate and adversely affect performance and hygiene.
- Calibration: Adjust settings based on the type and size of the chickens being processed. Each machine may have different settings that need fine-tuning to optimize performance.
- Test Run: Conduct a short test run to verify that all components function properly. This can help identify any issues before you start plucking a larger batch.
By taking these preparatory steps, operators can mitigate problems and ensure a smooth workflow throughout the plucking process.
Safety Measures During Operation
Safety in poultry processing cannot be overstated. In an environment where machines and live animals operate closely, risks abound. Here are essential safety measures that should be embedded in the operational guidelines:
- Protective Gear: Always wear appropriate safety gear such as gloves, goggles, and non-slip boots. This is your first line of defense against accidental injuries.
- Emergency Protocols: Make sure all workers are well-versed in emergency procedures. Familiarize the team with the location of emergency stop buttons and first-aid kits.
- Proper Training: Continuous training sessions can keep everyone well-informed about new safety measures or technological advancements. Knowledge is power, especially when machines are involved.
- Regular Breaks: Fatigue can lead to accidents. Encourage regular breaks to help maintain focus and efficiency. A sharp mind is a safe mind.
"An ounce of prevention is worth a pound of cure"âemphasizing the importance of staying ahead of safety issues can save your operation from potential hazards.
Implementing these safety guidelines can significantly reduce risks, thereby safeguarding both workers and the welfare of the chickens being processed. In short, operational guidelines, from preparation to safety measures, are non-negotiable for anyone serious about poultry processing.
Maintenance Best Practices
Proper maintenance of chicken plucking equipment is not merely a formality; it is an essential practice that can significantly impact operational efficiency and the longevity of the machinery. When you invest in quality plucking equipment, you also commit to regular upkeep to ensure each component functions optimally. By adhering to maintenance best practices, poultry operators can minimize downtime and increase their return on investment.
The benefits of a robust maintenance routine extend beyond mere functionality. A well-maintained machine is a safe machine, reducing the likelihood of accidents or malfunctions that could lead to injuries or product loss. Moreover, consistent inspection and care can help identify issues before they escalate into costly repairs.
Routine Inspections
Conducting frequent inspections is a cornerstone of effective maintenance. This is where careful eyes can really spot the signs of wear and tear that could spell trouble down the road. Here are some key areas to focus on during inspections:
- Belts and Seals: Look for any signs of fraying or wear, as these can drastically affect performance.
- Electrical Connections: Loose or corroded connections can lead to failures. Make sure to check wiring and connections regularly to prevent electrical issues.
- Bearing Lubrication: Proper lubrication can keep machinery running smoothly. Check levels and apply grease according to manufacturer recommendations.
- Water Heating Elements: In water pluckers, ensure that heating elements are functioning as expected to prevent inconsistent plucking results.
Set a schedule for these inspections, perhaps every few weeks or at least before major operations. Documentation of these checks can also provide valuable insight over time, helping you track how your equipment ages.
Common Repairs and Troubleshooting
While regular maintenance can prevent many issues, sometimes troubles arise nonetheless. Understanding some common repairs and troubleshooting techniques can help get a machine back up and running smoothly.
Some typical problems that may surface include:
- Motor Issues: If the motor does not start or runs irregularly, first check the power supply and electrical connections. An overload can also trigger automatic shut-offs, so be mindful of the machineâs current load.
- Plucking Challenges: Disharmony in the plucking process often points to a need for adjustment in finger configuration or improper operation settings. Adjust and re-test until you achieve optimal results.
- Water Temperature Fluctuations: In water pluckers, inconsistent water temperature can hinder plucking efficiency. Make sure heating elements and thermostats are functioning correctly. If issues persist, it may mean replacing faulty parts.
The key to successful troubleshooting is to remain calm and systematic. Donât jump to conclusions; instead, follow the symptoms step-by-step. Knowing when to attempt a fix and when to call in a professional can save time, money, and hassle.
Investing time in maintenance and repair can lead to longer equipment lifespan and improved performance, directly impacting your profitability in poultry processing.
In summary, establishing a regimented approach to maintenanceâfocusing on routine inspections and proactive troubleshootingâwill keep chicken plucking equipment operating at peak performance. By embedding these practices into daily operations, poultry farmers can enhance productivity, ensure worker safety, and maintain the quality of their products.
Emerging Technologies in Plucking Equipment
As the poultry processing industry evolves, the integration of emerging technologies has become crucial for efficiency and productivity in chicken plucking. This section will discuss the importance of automation and AI, along with the innovations in material and design that are shaping the future of chicken plucking equipment. By examining these advancements, we can understand the benefits they offer and the considerations that come along with their implementation.
Automation and AI in Poultry Processing
The potential of automation and artificial intelligence in poultry processing is immense. They redefine traditional methods, making the entire plucking process faster and more effective. Automated systems can handle the handling and plucking of chickens at a pace that human labor cannot match.
One of the significant benefits of automation is the reduction of labor costs. In the long run, investing in automated plucking machines can lead to substantial savings. This is especially true for large-scale operations, where wages can eat into profit margins. With machines executing the grunt work, farm owners can allocate human resources to more critical tasks like quality control and customer service.
Moreover, AI-driven systems bring precision and consistency that often elude manual methods. These machines are programmed to adapt their plucking techniques, ensuring that feathers are removed efficiently while maintaining the quality of the poultry. An example can be seen in Brand Zâs latest line of pluckers, which utilizes AI to adjust settings based on the type of poultry being processed, thus optimizing results for different breeds.
"Investing in automation is not just about saving time, it's about future-proofing your operation against labor shortages and increasing consumer demands."
However, transitioning to automated systems does require a certain level of expertise from operators. Therefore, training is essential. Understanding how to maintain and troubleshoot these machines is crucial, as neglecting this aspect can lead to inefficient operations.
Innovations in Material and Design
Alongside automation, innovations in material and design are also pivotal in transforming chicken plucking equipment. Manufacturers are increasingly using advanced materials that ensure durability and efficiency in operations. For instance, the introduction of lighter yet sturdier materials in the construction of plucking machines enhances portability and prolongs the lifespan of the equipment.
Furthermore, the design of plucking machines is becoming more user-friendly. Ergonomic designs not only prioritize the operatorâs comfort but also streamline workflow in processing facilities. This design shift is reflected in the intuitive configurations of new machinery, allowing for simpler adjustments and quicker maintenance.
One noteworthy advancement is the development of modular components that can be easily replaced or upgraded. This innovation allows farms to keep their equipment relevant without the need to purchase entirely new machines as technology evolves.
Moreover, environmentally sustainable materials are being adopted in the manufacturing of plucking machines, responding to the growing demand for eco-friendly practices within the industry. By using materials that minimize environmental impact, farms can contribute to sustainable poultry production while also appealing to a more conscientious consumer base.
In summary, emerging technologies in chicken plucking equipment pave the way for more efficient, reliable, and sustainable poultry processing. As the industry shifts, those who embrace these advancements can position themselves competitively in the evolving marketplace.
Environmental Impact of Plucking Processes
Understanding the environmental impact of plucking processes is crucial in today's poultry industry landscape. As the demand for efficiency grows, it becomes increasingly important to evaluate how the equipment and methods used affect the environment. From resource consumption to waste generation, the poultry processing sector faces scrutiny over its environmental footprint.
A thoughtful approach not only enhances the sustainability of the operations but also positively affects public perception and compliance with regulations. Operators need to consider energy use, water consumption, and waste management when selecting equipment and implementing processes.
âSustainability isnât just a buzzword; itâs necessary for the future of poultry farming.â
Efficiency in plucking, when balanced with environmental responsibility, can lead to significant reductions in greenhouse gas emissions and a smaller carbon footprint. Therefore, the integration of sustainable practices into plucking processes is an opportunity, not just a requirement.
Sustainable Practices in Poultry Processing
Sustainable practices in poultry processing involve a range of strategies designed to minimize the environmental impact while maximizing productivity. These practices can include:
- Energy-efficient machinery: Utilizing plucking machines that consume less power can greatly reduce operating costs while simultaneously lowering emissions. Modern drum and finger pluckers are designed to be more energy-efficient compared to older models.
- Water conservation: Water pluckers require substantial water use, thus developing systems that recycle and filter water can reduce freshwater consumption significantly. Implementing closed-loop systems helps maintain water quality and minimizes waste.
- Biodiversity support: Ensuring that the sourcing of chickens respects local ecosystems supports biodiversity. This means avoiding deforestation and over-exploitation of natural resources.
These measures not only address environmental concerns but also enhance the operational efficiency, potentially leading to cost savings and improved profit margins.
Waste Management Solutions
Proper waste management is an essential aspect of minimizing the environmental impact of poultry plucking processes. Effective management strategies can involve:
- Recycling Feathers and Byproducts: The feathers collected during plucking can be processed into animal feed, compost, or even biofuels. Utilizing these byproducts reduces waste and promotes the circular economy.
- Composting: Establishing composting systems for organic waste allows for the transformation of leftover materials, reducing the overall waste footprint. Composting not only helps manage waste but also enriches soil health.
- Waste Segregation: Implementing a system for separating different types of waste (organic, recyclable, hazardous) streamlines the disposal process. Efficient segregation allows for targeted recycling and proper treatment of hazardous materials.
- Educating Staff: Training staff in efficient waste handling practices can improve overall waste management quality and efficacy. When everyone on the team understands their role, compliance becomes easier.
By adopting these waste management solutions, poultry processing operations can significantly mitigate their environmental impact while contributing to a more sustainable future.
Regulatory Standards and Compliance
In the world of poultry processing, regulatory standards and compliance play a pivotal role in ensuring both safety and efficiency. These guidelines are designed not only to protect consumers but also to promote ethical practices within the industry. Failing to adhere to these regulations can lead to some serious repercussions, including legal actions and damage to business reputation.
Understanding Industry Regulations
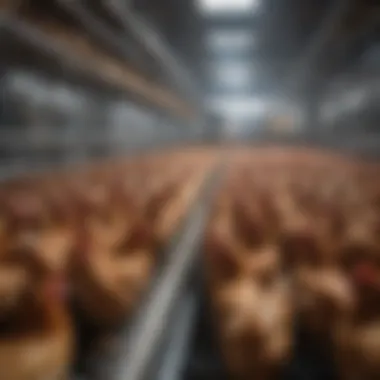
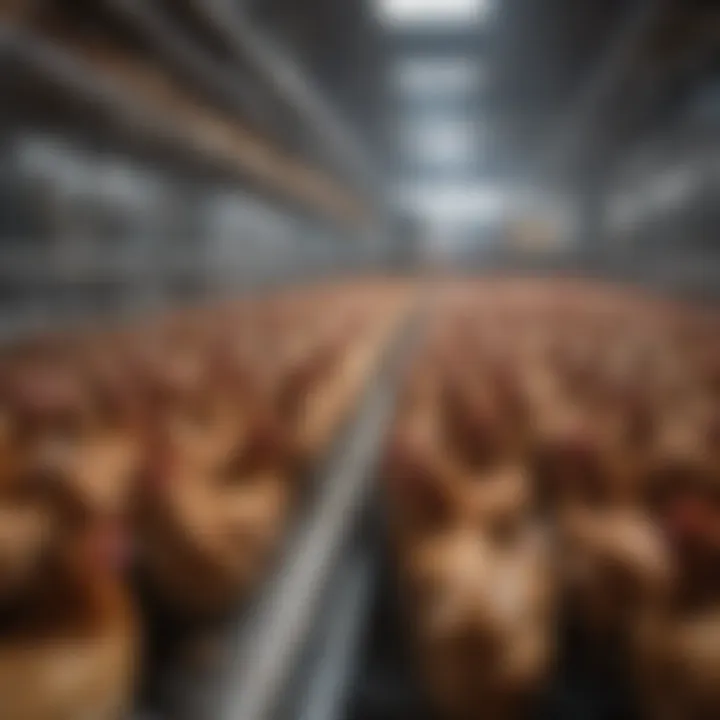
Navigating the maze of industry regulations can sometimes feel like trying to find your way in a labyrinth. The regulations often dictate how equipment should be designed, manufactured, and maintained. For instance, the USDA (United States Department of Agriculture) has stringent guidelines about the safety and operation of poultry processing equipment.
- Sanitation Standards: Equipment must be built in a way that enables easy cleaning. This helps prevent contamination, which is a serious concern in poultry processing.
- Material Requirements: The materials used for manufacturing must be food grade, preventing leaching that could harm the birds or contaminate the meat.
- Safety Protocols: There are regulations regarding the protection of workers who operate these machines, ensuring they have necessary safety gear and training.
A solid grasp of these regulations not only helps maintain compliance but also boosts consumer trust.
Certification Requirements for Equipment
When it comes to certification, itâs more than just a stamp of approval. It signifies that the equipment meets established standards, which is crucial for any poultry business looking to thrive in a competitive market.
Certain benchmarks must be met to obtain certification:
- Third-party Testing: Many regulatory bodies require equipment to undergo rigorous testing by accredited third-parties before they can receive certification. This ensures that the equipment performs as advertised.
- Ongoing Evaluations: Certification isn't a one-time deal. Regular inspections and evaluations are often necessary to maintain certification, ensuring equipment remains effective and compliant over time.
- Mark of Quality: Having equipment that is certified can serve as a strong marketing point, enhancing your reputation and attracting customers who prioritize quality and safety in their sourcing.
In summary, adhering to the regulatory standards and certification requirements is not just a box to tick; it is an integral part of running a responsible and successful poultry processing operation. As we explore the world of chicken plucking equipment, understanding these elements can empower farmers and processors to make informed decisions that benefit both their enterprises and their consumers.
Case Studies of Effective Use
Case studies of effective use provide critical insight into how chicken plucking equipment operates in real-world settings. By examining actual implementations, we can better appreciate the efficiencies gained and the challenges faced. These case studies shine a light on best practices, encouraging others in the poultry industry to adopt more productive techniques. They also reflect on the adaptability of different machines to varied scales of operation, showing that whether youâre a small farm or a large-scale poultry processor, there are suitable options available.
Successful Implementation in Small Farms
For small farms, the choice of chicken plucking equipment can significantly impact both labor and time efficiency. One striking example can be seen in the case of a family-owned poultry farm in Kentucky. This farm transitioned from manual plucking to a compact drum plucker, designed specifically for small operations.
- Benefits of Transitioning: The adoption of the drum plucker reduced plucking time from nearly an hour for each chicken to around 30 seconds. This swift improvement allowed for an increase in production ratesâmeaning farmers could meet market demand more effectively.
- Cost Management: The initial investment was justified as the reduction in labor costs over time led to a solid return on investment within just a couple of years. This case shows how smart equipment choices translate to profitability.
Moreover, the farmer noted that the plucker's ease of use meant family members, including younger generations, could engage in the business without needing extensive training. The advantages of having reliable equipment coincided with better product quality, ultimately enhancing their market reputation.
Large Scale Operations and Their Equipment Choices
On the other hand, large operations present a more complex scenario when it comes to selecting chicken plucking equipment. Take, for instance, a significant poultry processing facility operating in Arkansas. With thousands of birds processed daily, this facility opted for automated finger pluckers, which are renowned for their ability to handle high volumes without compromising quality.
- Mechanization for Efficiency: These automated systems allowed the operation to increase output substantially, processing up to 10,000 chickens in a single day. Each automated plucker worked in tandem with conveyor systems to streamline overall processing.
- Labor Considerations: While on the surface a larger investment may seem daunting, the facility managed to decrease labor costs by nearly 40%, minimizing human error and maximizing consistency.
- Maintaining Standards: The integration of sensors and monitoring systems further enhanced operational oversight, ensuring compliance with industry standards, a priority in poultry processing. This operational efficiency illustrates the necessity of proper equipment choices in achieving maximum productivity while keeping compliance in focus.
Comparative Analysis of Popular Brands
Understanding the landscape of chicken plucking equipment isnât just about knowing the different types. Itâs also crucial to dive into the brands that dominate this space. A comparative analysis of popular brands can shed light on their features, performace, and user satisfaction. Many farmers and poultry enthusiasts may find themselves at a crossroads when deciding which brand aligns best with their operational needs.
Each brand tends to have its unique selling propositions. Some excel in durability, while others may shine in technology and innovation. Through a comparative lens, we can evaluate specific elements such as reliability, customer support, and the overall value that different brands provide. This section will carefully dissect two of the leading names in chicken plucking equipment, allowing operators to make an educated choice.
Brand vs. Brand Y
When it comes to picking between Brand X and Brand Y, the decision can be quite nuanced. Both brands have carved their niches, but they cater to different types of users. Letâs break down their key characteristics:
- Brand X
- Brand Y
- Reputation: Generally regarded for its sturdy build.
- Features: Often equipped with advanced motor systems that offer consistent performance for long hours.
- Target Audience: More aimed at larger poultry operations that prioritize efficiency.
- Reputation: Known for its innovative design and compact size.
- Features: Incorporates user-friendly controls and lightweight mechanics, making it easier for small farm applications.
- Target Audience: Suited for smaller operations and those new to poultry processing.
"Choosing the right equipment can mean the difference between a good day and a great day in the field. Itâs not just about price; itâs about how well the machine fits your unique needs."
Customer Reviews and Feedback
Customer feedback plays an indispensable role in understanding the real-world performance of chicken plucking equipment. Insights gathered from users can highlight both strengths and weaknesses that arenât always apparent from technical sheets alone.
- Positive Reviews
- Critiques and Suggestions
- Many users praise Brand X for its robustness, and how it significantly cuts down plucking time. Testimonials often emphasize reliability in performance during peak operation hours.
- Conversely, Brand Y gains points for its ease of use. Comments from novice operators frequently remark on how user-friendly the features are, making it less daunting for someone just starting.
- Some users of Brand X have noted that its weight can be cumbersome during setup compared to more compact models.
- Similarly, Brand Y has encountered criticism regarding its longevity. While it works great initially, some users question whether it can withstand heavy usage over time.
Through examining both subjective and objective reviews, one can get a clearer picture of how these brands stack up in the field. Ultimately, the choice may hinge not only on the immediacy of features but also on long-term user experience.
Future Trends in Chicken Plucking Equipment
As the poultry industry continues to evolve, so does the technology surrounding chicken plucking equipment. The pressing need for efficiency, sustainability, and reduced operational costs is driving innovation across the board. This section aims to shed light on the new trends reshaping the future of chicken plucking, emphasizing why farmers and poultry enthusiasts must stay tuned to these developments.
Market Predictions and Consumer Behavior Trends
The landscape of poultry processing is shifting, influenced largely by consumer expectations and market demands. One noticeable trend is the rising emphasis on sustainability. Consumers today are becoming more socially and environmentally conscious. They increasingly prefer products sourced from farms that prioritize humane practices and sustainable methods.
"Tomorrow's consumers are not just looking for chicken; they're looking for how that chicken got to their plate."
Thus, equipment that minimizes waste is becoming favorable. For instance, more farmers are likely to invest in machines that efficiently process plucking while also addressing by-product utilization. This reflects an emerging consumer behavior that is predictive of future purchase choices. Understanding these shifts can prepare farmers to adjust their equipment selection accordingly.
Some other factors that are emerging include:
- Cost-effectiveness: The current economic climate is pushing operational costs to the forefront. Farmers are searching for machinery that offers better returns on investment.
- Quality assurance: A consistent and uniform plucking process is essential, as whole birds with intact skin fetch higher prices. As such, there's a shift toward equipment that guarantees these standards.
Technological Advancements on the Horizon
With innovation at the heart of technological advancements, new features are being integrated into chicken plucking machines, which could redefine operations in poultry processing. Some notable advancements to watch include:
- Increased Automation: Future machines will have smarter AI systems integrated, reducing the need for human intervention. This can lead to consistent, faster processing times, while minimizing labor costs.
- Advanced Material Use: There are going to be developments in materials that increase the durability of equipment. This also relates to having machines that are easier to clean and maintain, which is crucial in minimizing contamination risks.
- Smart Technology Integration: Expect to see IoT-enabled equipment that can provide real-time data analytics. This will help in monitoring machine performance, offering insights for predictive maintenance and increasing overall efficiency.
- Energy Efficiency: New machines are likely to operate on less power, showing a trend towards sustainability that aligns with consumer expectations. This allows operations to run longer hours without stacking up electric bills.
Staying ahead of these trends could mean the difference between thriving in a competitive market and merely getting by. Farmers need to consider how these advancements can be incorporated into current practices to optimize production and meet the evolving demands of consumers.
Epilogue
In the grand scheme of poultry processing, chicken plucking machines play a pivotal role. This article has explored many facets of this important equipment, shedding light on why understanding their operation is crucial for any farmer or industry player involved in poultry production. From manual options to sophisticated mechanical systems, the choice of plucking equipment can significantly impact the efficiency and quality of processing.
A few key elements are undeniably important when selecting chicken plucking equipment:
- Efficiency: The speed and thoroughness of plucking can directly affect productivity.
- Cost: Initial and ongoing costs must align with budget constraints, ensuring long-term sustainability.
- Maintenance: Understanding the upkeep required for the selected machines helps in planning and operation.
By considering these factors, farmers can optimize their poultry processing capabilities, enhancing the final product's overall quality. This, in turn, reflects positively on market competitiveness and consumer satisfaction.
Properly selected and maintained equipment ultimately leads to a smoother operation, less downtime, and increased profits.
Furthermore, as technology evolves, keeping abreast of advancements in plucking equipment can offer new opportunities for increased productivity, operational efficiency, and even sustainability.
Recap of Key Points
In this article, we have distilled various critical insights about chicken plucking equipment, including:
- The different types of equipment available, namely manual and mechanical options, and their respective pros and cons.
- An examination of the mechanics behind plucking machines, emphasizing their key components such as motor systems and configurations.
- Factors to weigh when selecting suitable equipment, highlighting brand reputation, budget, and ease of use.
- Essential guidelines for safe operation and maintenance best practices to prevent costly repairs.
- Insights into environmental impacts and the importance of sustainable practices within poultry processing.
- An overview of emerging technologies and how they shape the future of chicken plucking machinery.
Final Thoughts on Choosing Equipment
Choosing the right chicken plucking equipment isn't just about what looks shiny and new; it requires a thoughtful approach. Farmers must evaluate their specific needs against the features of the machine. What works wonders for a large-scale operation might be cumbersome for a small family farm and vice versa. Prioritizing ease of use can save time and effort, while considering long-term operational costs ensures that the investment doesn't become a financial burden down the road.